People often say, “new is always better”. And surely in a number of cases, new changes are equal to development. Regarding the field of logistics and supply chain, this term remains debatable but there is no doubt that an outdated system can reduce the effectiveness of logistics functions and more importantly, it easily poses a threat to the business.

However, it is true that making the decision to change is tough since abandoning the whole old system is somehow too risky for the business. Thus, finding signs to see whether creating changes is necessary or not can be based on these 3 signs.
So, let’s have a look to see whether these below lines are somehow familiar to you.
1. “Well it is quite confusing now, but trust me it will make sense”

Difficulties in describing thoroughly the logistics system to the new staff is considered as the first sign. When all the over-explanation keeps happening and what the manager gains back is the perplexed reaction from the new hires.
“Yeah, it’s confusing now, but it will make more sense over time?”. The line is used on a regular basis to reassure new employees, but ironically, over time, even senior staff start becoming confused by repeatedly answering the same questions about where to go for a piece of data or how to locate a particular shipping record. This is one of the most common scenarios for business, especially those that are turning into the growth phase.
2. “We just missed the KPI, didn’t we”
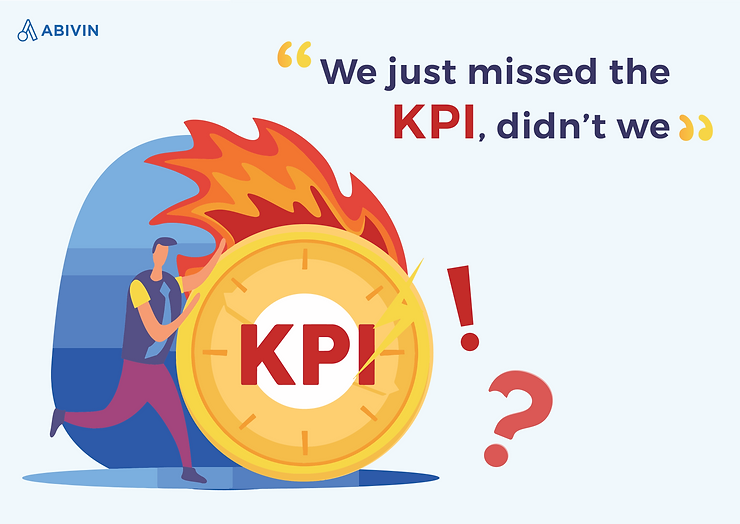
Scary, isn’t it? During the process, especially in the fields that KPI is extremely important to measure production, costs, and quality rates of a team, missing a KPI becomes a nightmare for every logistics manager. For example, for On-Time Final Delivery KPI, If the report is below 98% then operations are suggested to review the whole process and find solutions for improvement and efficiencies [1].
Missing KPI is understandable since even the best shipping teams miss a delivery deadline. However, a great frequency of these lapses is definitely a sign that the existing shipping environment lacks the bandwidth to accommodate growing order volumes.
3. “We don't know yet, but we will inform you about the Delivery Information asap”.
“A lot of things in this world are partial, but the priceless gift that everybody might own equally is 24 hours per day”. And perhaps, not everyone is willing to throw a precious day of their lives to do nothing but wait for the information of their parcel. Therefore, quick and accurate responses become a factor to build prestige, reputation, reliability, as well as customers' satisfaction.

If the logistics or delivery process is at all manual involving hours for staff to tell a customer delivery information, then the companies have their clue that it may be time to update the shipping practice.
Know what to change, but how?
For the first scenario, the problem is rooted in the lack of a clear working flow. Consequently, human resources are wasted on many steps of the process, from training to real-time working. Thus, before having any big changes, companies should make sure their team is moving the right wheel at the right time by redefining their standard operating procedures. With a good SOP, staff will have a clear working direction - a step-by-step process on how to get work done.
In the era of technology, robots are able to save a considerable amount of time and effort thanks to the elimination of manual interference. To understand better, take a look at a real case study from LightBulbs.com
Initially, LightBulbs.com owned six shipping workstations, all with standalone, carrier-provided shipping software. The workload was massive and cumbersome as the processes were manual when staff had to enter orders in multiple carrier systems, type in the dimensions of every package, and then choose the best carrier rate and service. And when holiday seasons came with doubled workloads, shipping became their biggest bottleneck.
To solve this problem, LightBulbs.com implemented a Transportation Management System (TMS) for parcel shipping, gaining the ability to load all carriers onto one platform and automating carrier rate shopping and shipment processing. As a result, LightBulbs.com succeeded in streamlining and increasing shipping orders completion.

Alongside the above software solution used by LightBulbs.com - TMS (Transportation Management System), many other systems/ technologies could be embraced to the delivery practice to meet all KPIs.
Demand Forecast Software or Advanced Planning and Scheduling: This will help logistics managers to create optimized schedules balancing production efficiency and delivery performance. Moreover, based on predicted demands or scenario data-driven decision making, companies can have a more precise market trend prediction and higher customer satisfaction.
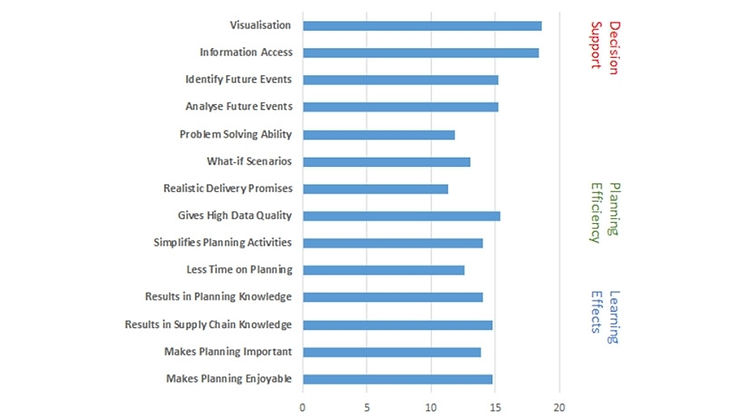
Warehouse Management System: WMS can avoid inaccurate inventory prediction, lack of knowledge about inventory location, redundant processes, etc. Using WMS companies can determine where to keep certain materials, products, and equipment to optimize the flow of their warehouse [2].
It is a dream for any logistics company if they have the advantage of knowing immediately when delays or transit exceptions, etc happen, so that companies can adjust accordingly. To fulfill their dreams, many technologies are now developed to enhance delivery practice faster and more precise:
Route Optimization Software: through solving the Vehicle Routing Problem and adequate route scheduling, ROS boosts operational efficiency. Besides, businesses can track products at every stage in the process until it gets to the consumer.
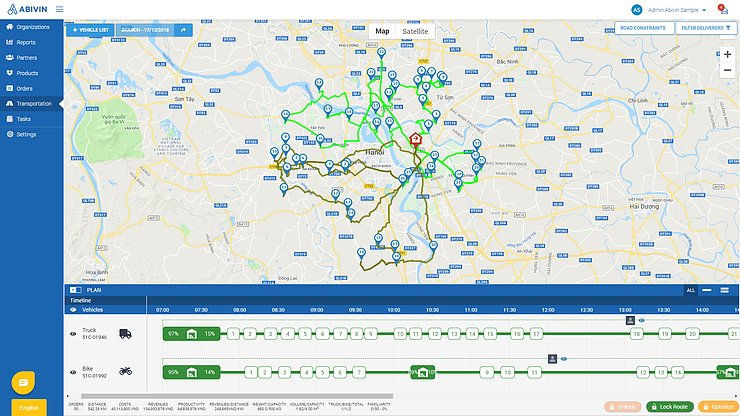
Telematics technology: By allowing users to collect data in real-time from vehicles, including details about location and condition, Telematics provides greater visibility of where vehicles are at all times to coordinate and schedule timely deliveries [3]
Order Processing Software (OPS): it helps a business to process more orders quicker and faster and allows customers to self-service their order and delivery information, payments. So that they can reduce days and monitor orders with real-time detail reports and dashboards. [4]
Indeed, saying goodbye is never easy, especially since it is the friend the company has been cooperating with for such a long period. After all, it has brought the firm to where it is today. The shipping practices have served the company well, but it can be improved to be better. So if any of these three signs are familiar, it’s probably time to consider changes for the delivery practice.
3 Signs It’s Time To Change Your Delivery Practice