The food and beverage (F&B) industry faces many unique challenges, from long lead times for raw materials and fluctuating prices to demanding safety and quality requirements and rapid changes in consumer behaviors [1].
To succeed in today's hyper-competitive market, F&B businesses must build a strong foundation for their supply chains. In addition to being managed by knowledgeable and experienced people, supply chains should be driven by flexible and unified systems.
Today, Abivin will share six success factors in managing the F&B supply chain.
1. Demand Forecasting
Demand forecasting uses past sales data to determine future consumer demand [2], aiming to support many important business activities such as budgeting, financial planning, production plan, raw material planning, etc.
First of all, accurate forecasts provide essential information about raw material inventory levels, work in progress, and desired output. These help businesses reduce the Bullwhip effect across the entire supply chain, resulting in optimized production and inventory levels and reduced stock-outs or overstocks.
Besides, demand forecasting also helps businesses improve the quality of customer service. Optimized inventory levels and improved distribution planning help businesses increase vehicle fill rates and on-time deliveries [3].

Businesses should first collect historical data on product demand, orders, delivery times, inventory, sales per month, per quarter, etc. Based on those data, enterprises choose appropriate demand forecasting methods such as judgment, market experiment, cause-and-effect relationship, and timeline. For example, the market experiment approach is most effective when a business is about to launch a new product, while the cause-and-effect approach focuses on determining why consumers buy the product [2].
2. Inventory Management
Inventories are lists of materials and products that are kept in a warehouse. The value of inventory can account for one-third to one-half of the business’s total assets. Therefore, effective inventory management helps the company always reserve the right amount of goods, not storing too much to cause capital stagnation or too little to interrupt the production process. As a result, businesses can significantly save time and money and promptly respond to customer needs.
Inventory management software is the most suitable solution for businesses. Companies can automatically control products and goods in stock and monitor export and import activities effectively.

However, finding the right inventory management software is not easy. Here are three characteristics that companies should keep in mind:
Inventory management software can manage customers, suppliers, warehouses, and inventory in different sales channels.
Inventory management software provides end-to-end track & trace: from when receiving the order to the time the goods are shipped.
Inventory management software can handle real-time workflow and real-time reports, indicators of productivity, inventory status.
3. Time-phased Replenishment Planning
The replenishment plan predicts demand, supply, and inventory levels over a specific period to determine how much material to buy and how much product to make. For example, if shippers always deliver raw material on a particular day of the week, planning for this material should follow the same cycle as the day it arrives.

In particular, Materials Requirement Planning (MRP) is an inventory management software that helps businesses calculate the number of materials needed before production or purchase.
Firstly, MRP helps businesses plan additional production to supply goods to customers promptly. Second, when setting up MRP, managers will control orders of input materials, avoiding excess when entering warehouses or inventory left for too long and unusable [4].
The MRP process consists of three main steps [5]:
- Manage the number of available ingredients
- Determine the number of supplement ingredients
- Schedule production or purchase
4. On-demand Manufacturing Planning

In some F&B businesses, manufacturing factories operate independently from the rest of the supply chain. F&B factories often use a lot of capital to maximize output. However, an excessive focus on production efficiency can lead to a much larger supply than demand and failure to meet specific customer needs [1].
As a result, on-demand production is a reasonable solution for businesses. It is a production plan based on actual orders, which helps firms effectively utilize resources, costs, and time to produce real value. Production planning, production processes, and material flow coordination are synchronized between manufacturers and carriers, distributors, etc. Enterprises can also connect with customers and improve service quality.
5. Supply Chain Master Data Management
Thanks to the fast growth and increasing complexity of the F&B industry, the existing systems of enterprises cannot provide enough broad and deep data for supply chain planning and optimization. At this time, businesses should employ the Enterprise Resource Planning (ERP) system to manage their master data.
ERP system is a multi-functional, multi-department management software solution that helps businesses collect, store, manage and analyze data from their business activities, including planning products, costs, production or service provision, marketing and sales, delivery, and payment [6].

Data from all parts of the enterprise will be managed and connected in a unified system; therefore, businesses can retrieve them fully, quickly, and promptly. Moreover, by using a one-in-all system, companies can quickly detect and resolve problems, reduce decision-making time, improve existing services, and increase customer satisfaction. Some examples of ERP systems are Microsoft Dynamics, Oracle e-Business Suite, SAGE, SAP Business One, etc.
6. Sales and Operations Planning (S&OP)
If production planning helps F&B businesses balance supply and demand quickly, sales and operations planning focuses more on the long term. The S&OP process integrates information from sales, production, finance, marketing, shipping, and procurement, helping managers analyze and make quick decisions. In some cases, S&OP also allows them to compare and evaluate multiple situations, prepare contingency plans to avoid risk, and stay ahead of the competition if the market changes [1].

The S&OP process consists of 5 main steps [7]:
1. Product strategy selection: Managers analyze and evaluate the feasibility of new product launches and consider whether to reduce or stop selling any products.
2. Demand analysis: In this step, managers predict more precisely the demand for the product, such as the number of orders, shipments, etc. to make qualified sales and operations planning, and at the same time, those predictions also form the basis for the analysis and evaluation of the effectiveness of their campaigns to come up with a reasonable solution.
3. Supply capacity assessment: To meet the demand in step 2, enterprises need to consider their production capacity and inventory management: whether the supply of goods is enough and promptly meets the additional demand if the market changes.
4. Financial calculation: Finance plays a vital role in keeping the S&OP process running smoothly. Predicting and analyzing specific financial figures will help businesses calculate reasonable costs for their plans.
5. Action plan: Finally, the business needs to develop an action plan. In addition to the list of specific tasks that need to be implemented, the plan also needs to consider different supply and demand scenarios and a response plan to risks if the product is of poor quality, the demand increases/decreases than expected, etc.
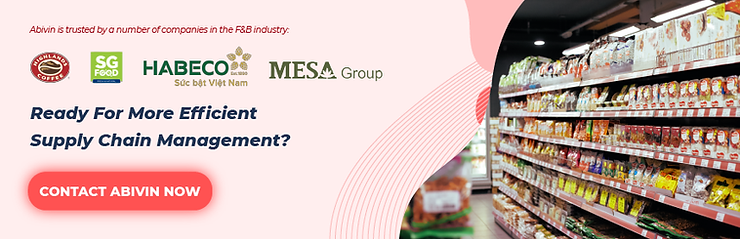
References
[1] https://www.logility.com/blog/six-must-have-supply-chain-capabilities-for-success-in-the-food-and-beverage-industry/
[2] https://www.wikihow.vn/D%E1%BB%B1-b%C3%A1o-nhu-c%E1%BA%A7u-th%E1%BB%8B-tr%C6%B0%E1%BB%9Dng
[3] https://blog.arkieva.com/demand-forecasting-for-supply-chain-management/#:~:text=Demand%20forecasting%20forms%20an%20essential,all%20supply%20chain%20related%20decisions.&text=Demand%20Forecasting%20provides%20an%20estimate,purchase%20in%20the%20foreseeable%20future.
[4] https://antonierp.wordpress.com/2018/07/27/mrp-la-gi/
[5] https://searcherp.techtarget.com/definition/material-requirements-planning-MRP#:~:text=Material%20requirements%20planning%20(MRP)%20is,scheduling%20their%20production%20or%20purchase.
[6] https://gsotgroup.vn/he-thong-erp-la-gi-va-no-hoat-dong-nhu-the-nao.html
[7] https://www.cask.vn/tin-chi-tiet/quy-trinh-5-buoc-de-doanh-nghiep-thuc-hien-thanh-cong-s-op
6 Success Factors In Managing The F&B Supply Chain