Due to the coronavirus outbreak, businesses have witnessed disruptions and rapid fluctuations of supply chains on a global scale. In that context, what value can technology bring to enterprises?
Businesses can improve the operational continuity of the food and beverage (F&B) supply chain thanks to the power of technology. It can help manufacturers and retailers stand firm against negative market trends to track and trace and ensure transparency in the process quality.
Below are suggestions for top solutions that food and beverage companies should consider to deal with their operational difficulties.
1. Prioritize using the software as a service (SaaS) operating on a cloud-based platform

When investing in supply chain technology, businesses should consider a cloud platform or software as a service (SaaS). Why? Unlike on-premises, cloud-based solutions offer outstanding advantages, including rich features, the ability to connect to other platforms, data security, the low total cost of ownership (TCO), etc. [1] For supply chain operations, popular logistics solutions include transportation management software (TMS), warehouse management software (WMS) and asset management software (AMS), along with real-time visibility, demand planning, and inventory management.
With the above benefits, the use of SaaS can help F&B businesses save logistics costs to focus on production, thereby ensuring competitive prices to generate more revenues.
If your business manages multiple manufacturing factories or warehouses, cloud-based inventory management or asset management solutions will also offer tremendous advantages. For example, the information of perishable items such as seafood, fresh milk, or product ingredients will be recorded regularly to be handled promptly before spoiling.
2. Adopt a cold chain management solution

According to a 2018 report by CEL consulting, Vietnam's agriculture industry loses about 8.8 million tons of food each year, equivalent to US$3.9 billion, due to inefficient transportation management. Besides, the report also shows that only about 14% of manufacturers use cold chain management solutions.
Leaders need to change their perspective on cold storage technology solutions. The Vietnam Economic Times in 2019 suggested that businesses should consider cold chains as an asset, not an expense [3]. As mentioned above, F&B companies can fully invest in temperature monitoring systems for their products to limit damages. Technology options in the cold chain are also quite diverse: from temperature sensors and remote temperature control devices to telematics devices with transportation management platforms.
Learn more about how to solve the problem of changing cold supply chains in Vietnam.
Investing in equipment to monitor and store cold goods for each pallet or shipment will cost a lot. As a result, leaders may consider spending a fraction of the cost working with third-party logistics providers (3PLs). The advanced temperature-monitoring technologies of these partners can then be integrated and performed on a cloud platform at a lower cost.
3. Use solutions to increase visibility
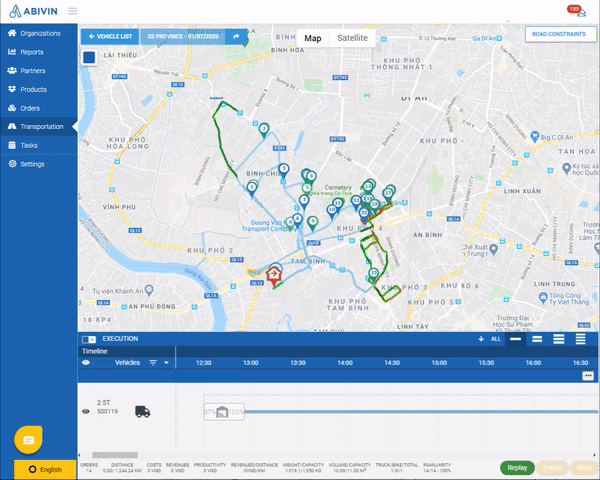
No matter how businesses choose to monitor the cold supply chain, damage to goods and loss in transportation can always occur, especially under force majeure circumstances such as pandemics or inadequacies in border policy. At that time, the time-consuming process of retrieving damaged goods can be a big challenge for businesses in the food and beverage industry, besides the financial loss. Similarly, reconciling purchase invoices, receipts, and related documents can also cause loss of time when they are not digitized in the first place.
A practical solution to these pain points is Supply Chain Visibility Solutions. These kinds of software will optimize the supply chain for businesses thanks to managing vehicles in real-time, digitizing documents, and providing reports on logistics activities.

Solutions to increase track and trace capabilities can help F&B businesses confirm documents or delivery and receipt addresses in just a few minutes. As a result, companies can save thousands of hours each year caused by waste in the traditional way of working. In addition, the real-time visibility will also eliminate fraud in the books or declaration of costs incurred in logistics activities.
4. Employ software solutions suitable for the characteristics of the industry

Food and beverage companies include beer, wine to prepackaged or pet food because all of them face fierce competition on supermarket shelves and the challenge of consumer demand.
However, whether they are retailers, shippers or manufacturers, each needs an entirely different technology. The brewing process will be different from the coffee-making process. The hygiene and ingredient quality requirements in baby food production will undoubtedly be much more stringent than in pet food production. Therefore, F&B businesses should consider partnering with software vendors with expertise in addressing the unique needs of their production and supply chain operations.
Properly deploying technology platforms will also be a big challenge for businesses because no fixed roadmap can suit every market strategy, competitive situation, or investment budget. However, leaders can always reduce the cost of ownership and easily track return on investment (ROI) once a sound digital transformation strategy is in place.
Conclusion
Reasonable investments in technology will help reduce costs and working time for F&B businesses, scale-up production with less labor, or allow companies to reach new consumer groups and markets to increase profits. In terms of investments in software, leaders need cloud platforms that can track shipments, control inventory, manage fleets, and, most importantly, digitalize and automate manual work that is cumbersome and contains many risks of fraud.
Abivin vRoute is a flexible transportation management platform that can meet the above diverse needs. Enterprises can also easily integrate Abivin vRoute with existing ERP systems or telematics devices to ensure real-time visibility over their supply chains.

Contact us now for a free trial of Abivin vRoute - The proprietary Dynamic Route Optimization and Transportation Management System
Supply Chain Technologies For The F&B Industry