ABC analysis of inventory is the classification of a group of items in decreasing order, based on their value to the business. The A group is the most important in terms of the value contributing to the company, whilst C items are the least valuable. To be more specific:
- Group A usually represents 10-20% by number of items and accounts for 50-80% of dollar volume
- Group C contains 60-70% of the items but only accounts for 10-30% of the dollar volume
- Group B has more items than group C but less than group A, with the value is higher than group C but far less than group A in volume
It is important to note that the inventory’s ‘value’ can be based on a number of criteria, such as annual sales revenue, profitability or even annual consumption value. With the help of ABC analysis, managers can focus their time on other valuable products and adapt their inventory control policies accordingly.

1. The 80/20 rule of ABC analysis
The Pareto principle or 80/20 rule, specifies that 80% of consequences come from 20% of the causes, asserting an unequal relationship between inputs and outputs. The principle holds that in general about 80% of effects are attributable to about 20% of causes: 20% of your accounts are likely to produce about 80% of the company’s revenue. In ABC analysis, 80% of a business’s annual sales value comes from 20% of its items such as category A items. Categories B and C then make up the remaining 20%. How this 20% be split between category B and C will vary, based on a business’s product portfolio.
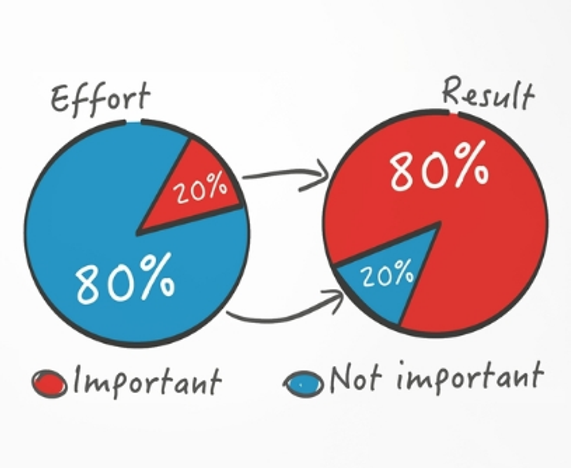
2. The application of ABC analysis
ABC analysis is a simple framework to work out which items in the warehouse are the most important, and, should therefore consume most of the time spent for stock control and management. The ABC inventory analysis is used primarily for 3 main tasks:
- Determining the levels of safety stock to maintain, in order to avoid stock outs in critical SKUs
- Providing appropriate levels of inventory counting, in which priority items may be counted more frequently, or automatic counting may be supplemented with manual checks
- Locating SKUs in individual warehouses and warehouse networks
For managers, revenue is the most common factor used to determine the ranking in ABC analysis. However, there are also other factors that could be used such as profit margin, customer importance, relationships to other items and velocity or returns. For profit margin, the return on items with a higher profit margin may justify higher inventory levels. Meanwhile fast-moving items may be maintained at a higher inventory levels because items with very low turns may have little or no safety stock.
Using ABC analysis can save time for inventory managers, helping them to work out appropriate inventory rules for each category. Thanks to different service levels, safety stock levels and re-ordering parameters for each category, managers can prioritize the management of policies based on their classification.
3. Drawbacks of traditional ABC analysis

Even though ABC analysis is a relatively easy way to classify and manage the company’s inventory, it also has a number of limitations. For managers who classify items based on one or two factors, the classifications might be one-dimensional and too simplistic. Having the ABC analysis in a traditional way can lack flexibility. In a marketplace where trends come and go and product sales can be erratic, items can move from category C to A very quickly. Without constant analysis, the company’s current ABC classification can quickly become obsolete.
In addition to the risk the group getting out-of-date quickly, it can be time-consuming to constantly re-evaluate and re-classify between the three groups. This will eventually affect the overall benefit of the company.
4. Solution
To overcome the disadvantages above and use the ABC analysis effectively, it is essential for managers to utilize software to analyze and categorize your inventory. Thanks to the help of technology, managers can keep track on the movement of items between the groups and automatically analyze the items based on numerous factors.
Click here to Manage Real-time Inventory Status with Abivin vRoute!
Preferences:
https://www.eazystock.com/uk/blog-uk/abc-analysis-inventory-management/
What Is ABC Analysis In Inventory Management?